Seals are the most fundamental and critical components ensuring the proper operation of hydraulic systems. In hydraulic and pneumatic systems, most leaks occur due to seal failure. The performance and reliability of O-rings and sealing devices are essential indicators of system design and manufacturing quality. Improper sealing can lead to internal and external leaks in components and systems, reducing volumetric efficiency. In severe cases, the system may fail to build pressure and become inoperable. Additionally, leaks can contaminate equipment and pollute the environment. Therefore, using O-rings correctly is crucial for ensuring the normal operation of machinery.
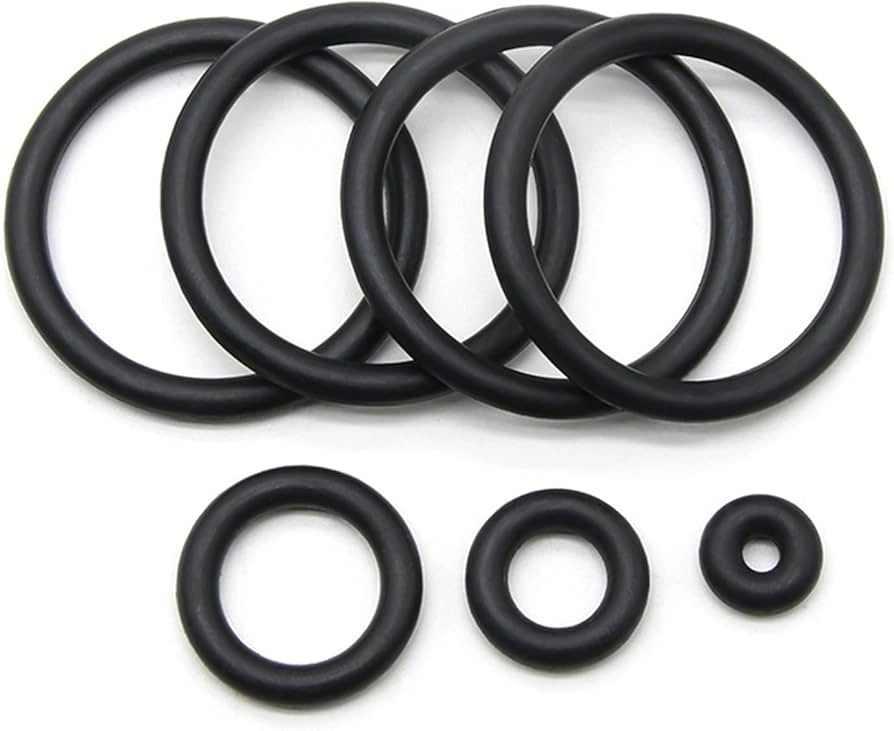
Main Causes of O-Ring Seal Failure
- Improper Seal Groove Design
- Incompatibility Between the O-Ring Material and the Working Medium
- Incorrect O-Ring Size Selection
- Insufficient Lubrication of the O-Ring
Since O-rings are subjected to complex forces, some failure causes may be difficult to diagnose. In such cases, material testing and environmental studies may be necessary.
Common Failure Modes and Solutions
1. O-Ring Becomes Flattened After Use
Causes:
- Poor elasticity and heat resistance of the seal material.
- The O-ring expands excessively and compressive force increases after prolonged exposure to the working medium in the hydraulic system.
- Incomplete vulcanization of rubber during production, leading to flattening under pressure.
Solutions:
- Use rubber materials with low coagulation properties.
- Select heat-resistant rubber materials (such as nitrile rubber or neoprene) to withstand friction-generated heat.
- Ensure that the O-ring material is compatible with the working medium and meets physical performance requirements.
2. O-Ring Wear
Causes:
- Common in seals with relative movement and vibration.
- Excessive roughness of the sliding surface causes premature wear.
- Excessively smooth sliding surfaces lead to poor lubrication.
- Contaminant particles in the oil system.
Solutions:
- Manufacture surfaces according to recommended roughness specifications.
- Ensure adequate lubrication during movement, especially internal lubrication.
- Use high-precision filters in the system.
- Choose wear-resistant O-ring materials, such as polyurethane rubber.
3. O-Ring Hardening and Oxidation Due to Heat
Causes:
- Operating temperatures exceed the material’s normal working range.
- Elastomers harden, plasticizers evaporate, and oxidation occurs.
- Small surface cracks perpendicular to the pressure direction appear, leading to local dents or cracks.
- Common in seals exposed to air or air pollutants.
Solutions:
- Use high-temperature and oxidation-resistant materials.
- Reduce the working temperature of system fluids.
4. O-Ring Extrusion, Nibbling, and Spiral Failure
Causes:
- Excessive sealing gap.
- System pressure exceeds the seal’s pressure resistance or lacks a backup ring.
- The seal material does not meet the required hardness.
- Incorrect groove dimensions or improper O-ring selection (oversized relative to the groove).
- Spiral failure results from poor concentricity, insufficient lubrication, or overly soft seal materials.
- When part of the O-ring slides while another part rolls, twisting or cracking occurs.
Solutions:
- Reduce the sealing gap.
- Select properly sized O-rings.
- Ensure that concentricity meets design requirements.
- Manufacture seal grooves according to standard specifications.
- Use reinforced composite seals or backup rings to prevent extrusion.
5. O-Ring Damage During Installation
Causes:
- Sharp edges in the seal groove or improper lead-in chamfering.
- Lack of lubrication during installation.
- O-ring gets cut, twisted, or pinched by sharp edges, resulting in surface dents, peeling, or flaking.
Solutions:
- Machine seal grooves according to design specifications, avoiding sharp edges.
- Apply lubrication to the groove and O-ring before installation.
- When inserting the O-ring through threads, cover the threads with a thin metal sheet or tape to facilitate smooth insertion.
Conclusion
O-rings are widely used in hydraulic components and systems due to their simple structure, ease of manufacturing, and reliable performance. This analysis by Rilong Rubber & Plastic Products Factory summarizes the working mechanism, failure modes, causes, and solutions for O-ring failures. By continuously accumulating experience and analyzing problems encountered in use, O-rings can be better applied in various industrial systems.
4o